Choosing the right adhesive for your industrial project can make or break its success. Whether you’re bonding metals in aerospace or assembling packaging in manufacturing, the adhesive must meet specific performance and environmental needs. This guide explains how to select between structural and non-structural adhesives, key factors to consider, and common pitfalls to avoid, ensuring your project is efficient and durable. At Gh1200, we specialize in high-performance adhesives tailored to your industry.
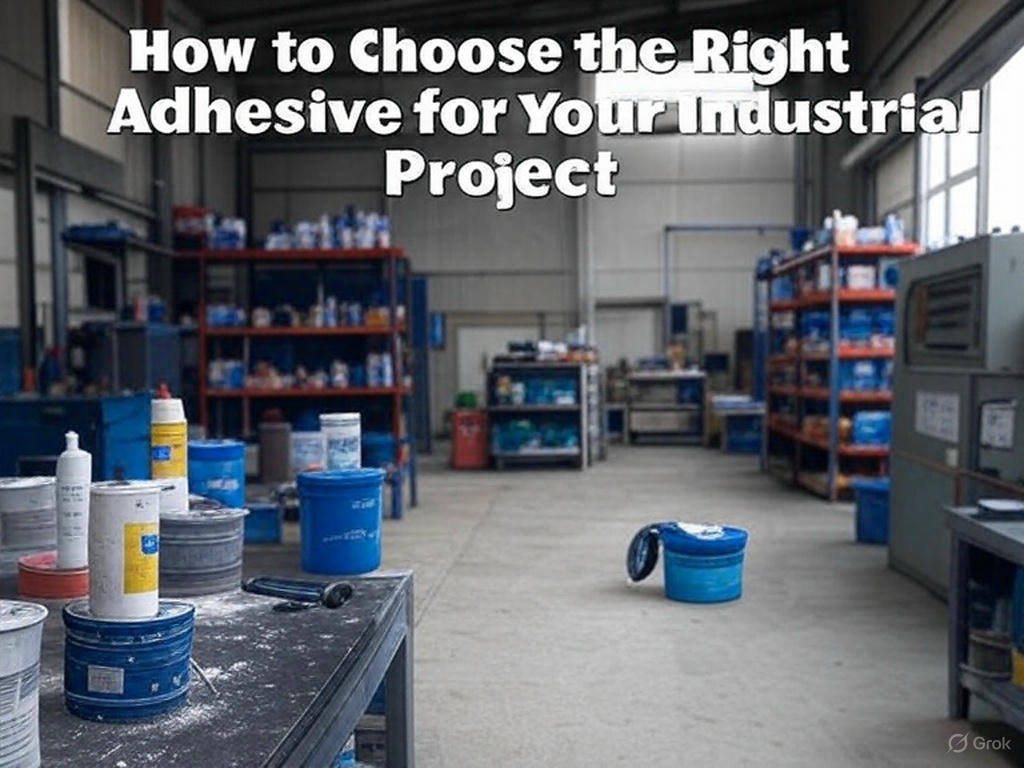
Key Factors in Adhesive Selection
Selecting an adhesive involves evaluating several critical factors to ensure it meets your project’s demands. Here are the top considerations:
- Material Compatibility: Ensure the adhesive bonds well with your substrates (e.g., metals, plastics, composites). For example, epoxy adhesives excel with metals, while cyanoacrylates suit plastics.
- Load-Bearing Requirements: Structural adhesives, like epoxies, support heavy loads in construction, while non-structural adhesives, like pressure-sensitive tapes, are ideal for lighter applications like labeling.
- Environmental Conditions: Consider exposure to heat, moisture, or UV light. Polyurethane adhesives resist moisture, making them suitable for outdoor construction.
- Curing Time: Fast-curing adhesives (e.g., cyanoacrylates) are great for high-speed production, while slower-curing epoxies ensure stronger bonds in aerospace.
- Application Method: Choose adhesives compatible with your process, such as sprayable adhesives for large surfaces or precise applicators for small parts.
Structural vs. Non-Structural Adhesives: When to Use Each
As explained in our Structural vs. Non-Structural Adhesives guide, structural adhesives bear significant loads, making them ideal for high-stress applications like bridges or aircraft. Non-structural adhesives, conversely, provide temporary or low-stress bonding, such as in packaging or automotive trim. Here’s when to use each:
- Structural Adhesives: Use for permanent, high-strength bonding in aerospace, construction, or automotive frames. Example: Epoxy bonding steel beams in a skyscraper.
- Non-Structural Adhesives: Choose for lightweight, flexible, or temporary bonds in packaging, electronics, or interior design. Example: Pressure-sensitive adhesives for product labels.
Learn more about high-shear adhesives for demanding applications.
How to Choose the Right Adhesive?
Follow these steps to select the perfect adhesive for your project:
- Assess Project Needs: Define the substrates, load requirements, and environmental conditions. For instance, a marine project needs moisture-resistant adhesives.
- Research Adhesive Types: Compare options like epoxy, polyurethane, or acrylic based on strength and curing time. Gh1200 offers a range of adhesives for diverse industries.
- Test Compatibility: Conduct small-scale tests to ensure the adhesive bonds effectively without compromising materials.
- Evaluate Safety and Regulations: Check for compliance with industry standards (e.g., FAA for aerospace, ASTM for construction).
- Consult Experts: Contact Gh1200’s adhesive specialists for tailored recommendations and product samples.
Common Mistakes to Avoid
Avoid these pitfalls to ensure a successful bonding process:
- Ignoring Curing Time: Rushing curing can weaken bonds. Allow adequate time, especially for structural adhesives like epoxies.
- Mismatching Materials: Using an adhesive unsuitable for your substrate (e.g., silicone on oily surfaces) leads to failures.
- Overlooking Environmental Factors: Exposure to heat or moisture can degrade adhesives if not accounted for.
- Skipping Surface Preparation: Clean and prime surfaces to maximize adhesion strength.
- Neglecting Safety: Follow handling guidelines to protect workers and meet regulations.
- Conclusion
- Choosing the right adhesive ensures your industrial project is strong, efficient, and long-lasting. By considering material compatibility, load requirements, and environmental factors, you can select the perfect structural or non-structural adhesive. Avoid common mistakes and consult experts to optimize your bonding process. Ready to find the best adhesive for your project? Contact Gh1200 for expert advice and high-performance solutions.
Conclusion
Choosing the right adhesive ensures your industrial project is strong, efficient, and long-lasting. By considering material compatibility, load requirements, and environmental factors, you can select the perfect structural or non-structural adhesive. Avoid common mistakes and consult experts to optimize your bonding process. Ready to find the best adhesive for your project? Contact Gh1200 for expert advice and high-performance solutions.
Frequently Asked Questions (FAQs)
What factors should I consider when choosing an adhesive?
Consider material compatibility, load-bearing needs, environmental conditions, curing time, and application method. For example, structural adhesives suit heavy-duty projects, while non-structural ones are better for lighter tasks.
How do structural and non-structural adhesives differ in selection?
Structural adhesives are chosen for high-strength, permanent bonds in industries like aerospace, while non-structural adhesives are used for flexible or temporary bonds, such as in packaging.
Which adhesive is best for bonding metal?
Epoxy or polyurethane adhesives are ideal for metals due to their high shear strength and durability. Test compatibility for specific alloys.
What are common mistakes in adhesive selection?
Common mistakes include ignoring curing time, mismatching materials, neglecting environmental factors, skipping surface prep, and overlooking safety.
How do environmental conditions affect adhesive choice?
Heat, moisture, or UV exposure can degrade adhesives. Choose moisture-resistant options like polyurethane for outdoor use or UV-stable adhesives for sun-exposed surfaces.